
Industrial Wastewater treatment
Meeting the highest environmental standards.
Treating industrial wastewater presents a unique challenge due to the diverse range of impurities it contains. Moreover, there is a continuous tightening of effluent standards. As a result, effectively treating industrial wastewater requires extensive knowledge of process technologies and their economical.
With our professional experience gained over the years, we possess the expertise to meet both customer requirements and mandatory regulations with utmost precision. Our goal is to achieve an optimal balance between efficiency and cost-effectiveness. This encompasses not only minimizing initial investment expenditure but also reducing operational costs throughout the lifespan of the treatment plant.
ADOX®
Advanced Oxidation
Oxidative removal of pesticides and VOC. Ground and surface water are frequently subject to organic pollutants such as pesticides and chlorinated hydrocarbons. In order to prevent health risks strict legislation has been passed.


“ADOX” stands for “ADvanced Oxidation” and represents a process which leads to the mineralization of organic pollutants in water by OH-radical oxidation.
The main principle of the ADOX®- process is the combined use of ozone and hydrogen peroxide. Ozone is produced in an ozone generator from air or oxygen and is added to a partial stream by an injector or diffusers in the reactor. Hydrogen peroxide is dosed into the main treatment line.
Subsequently, a high percentage of the pollutants is mineralized in the reaction tank. In the ADOX®- process post-treatment is accomplished by biological activated carbon filtration.
BIOPUR®
BAF – Biofiltration
BIOPUR® is a biofiltration system developed by WABAG for the biological treatment of wastewater. It utilizes biofilms, cultivated on solid surfaces, to biologically degrade pollutants in the wastewater, while simultaneously capturing suspended solids with filter materials. BIOPUR® is a modern and space-saving process capable of meeting the toughest water treatment requirements in both municipal and industrial contexts.
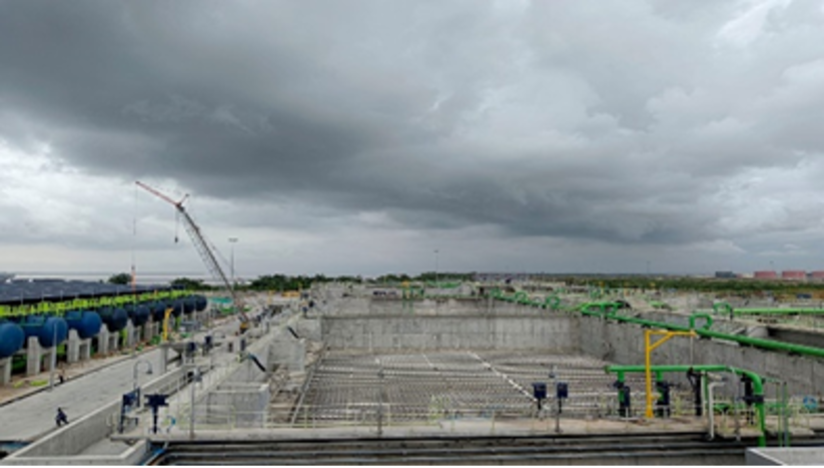
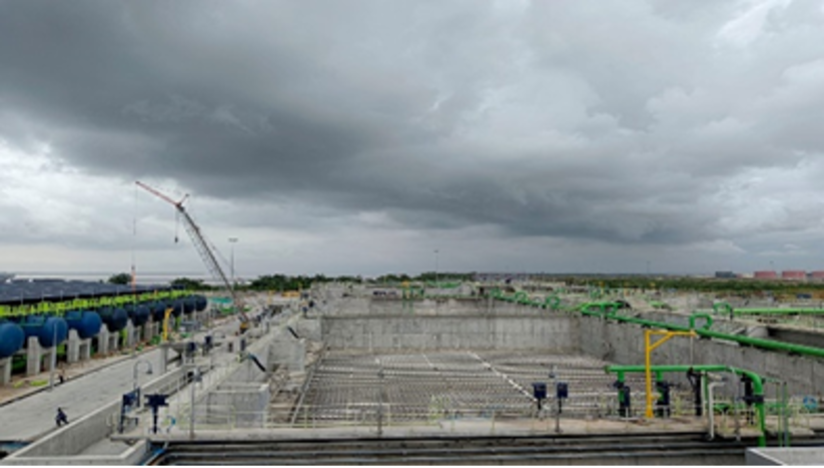
The carrier materials and filter media are precisely tailored to water treatment needs, making the system fully customizable for a multitude of applications. It can be effectively combined with other treatment methods such as tertiary filtration, making it ideal for plants tasked with removing micropollutants.
Key Features
•Highly compact
•Suitable for enclosed plants with minimum emissions
•Highly flexible in hydraulic fluctuations and organic load variations, especially when combined with other process stages è Highly automated operation
BIOZONE®
Combined chemical-oxidative and biological effluent treatment
The BIOZONE® process has been developed by WABAG for the treatment of effluent containing a high percentage of organic compounds, which are resistant to biodegradation.
The addition of ozone breaks up the complex compounds of e.g. micropollutants, which thereby lose their harmful effect and can be subsequently partially degraded by biological means. Reactive products from ozonation are removed in a downstream biological phase, preferably deep bed, bioactive filtration.
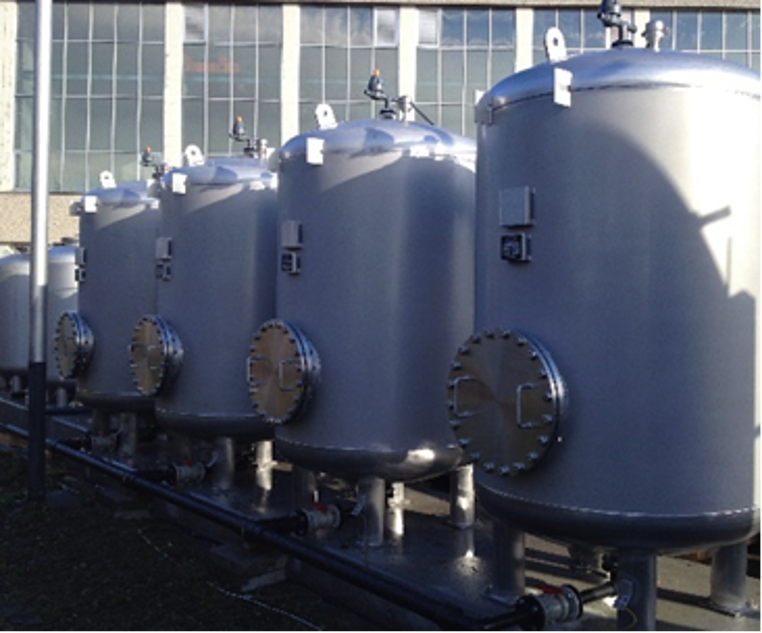
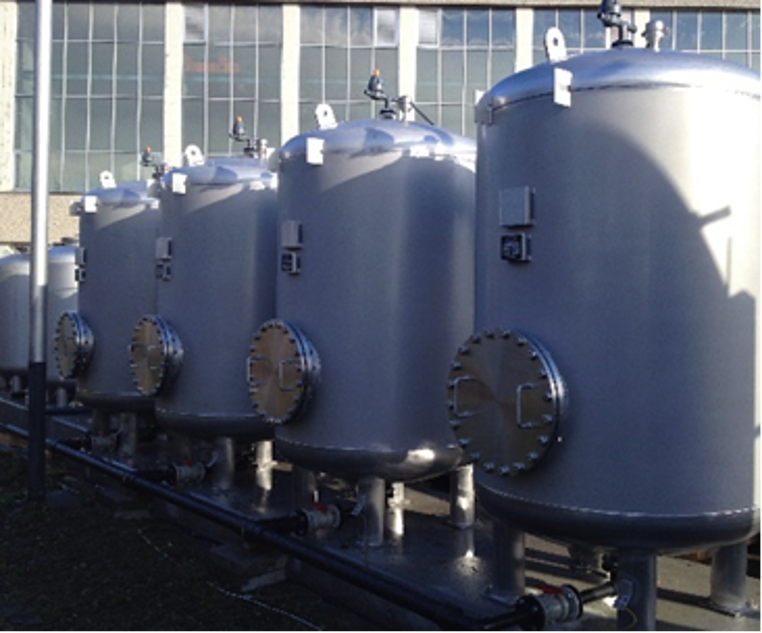
Key Features
•Compact process with limited space requirement
•Relatively low operating costs
•Robust process
•Simple operation
•No formation of residuals
•Extensive disinfection of the wastewater
CERAMOZONE®
Ceramic membranes combined with Ozone.
What makes the ceramic membrane unique is the nature of the material. In contrast to “normal”(organic) membrane fibers, which are quickly destroyed by ozone, ceramic membranes respond positively to any residual ozone in the water: the ozone contained within the water minimizes the fouling potential on the membrane surface. In a best-case scenario, there is no longer any need for chemically enhanced backwashing. This process has already been tested by WABAG on a pilot-project scale using different grades of water. The technology is now ready for use on a large scale.
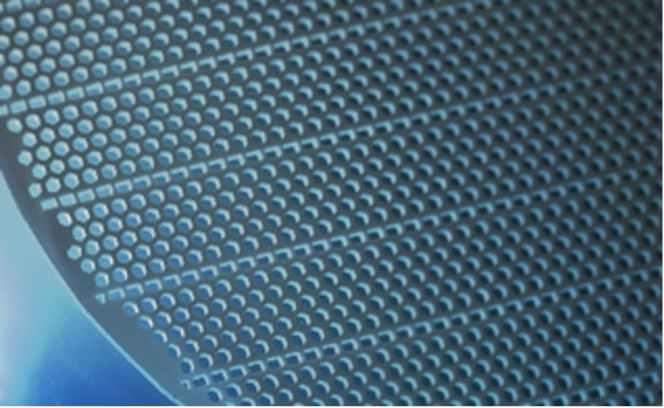
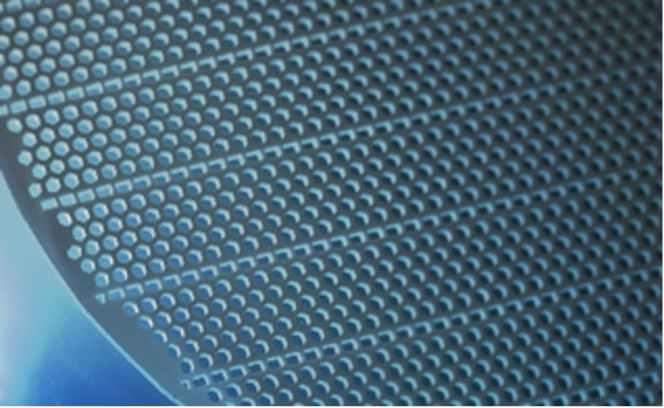
CYCLOPUR®
SBR (Sequencing Batch Reactor)
SBR (Sequential Batch Reactor) is a system for the biological treatment of wastewater. In contrast to conventional activated sludge processes, where wastewater undergoes treatment by passing through a series of tanks, the SBR method involves conducting different steps sequentially in the same tank. As the reactors are filled on a batch-by-batch basis, several SBR tanks and/or an influent buffer tank are required to treat wastewater continuously. On the other hand, there is no need for the recirculation equipment that typically accompanies continuous systems, and the cleaning performance can be flexibly and perfectly adapted to requirements.
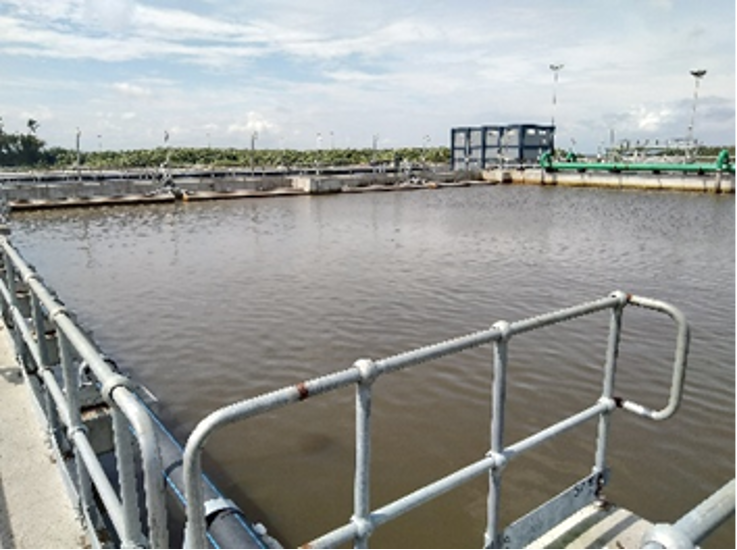
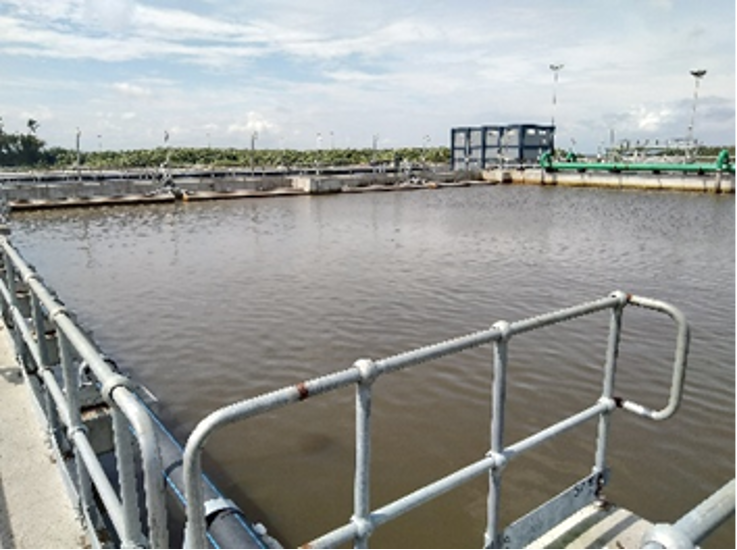
The typical steps involved in the process are:
•Fill (mixed or aerated)
•Reaction: aeration or mixing
•Sedimentation
•Decantation: extraction of the clean water
Special decanter. The WABAG swivel-joint decanter has been designed by drawing on a wealth of experience from various projects and is produced in-house by us. The model is in use at several plants. Its defining features include a maintenance-free stainless steel swivel joint and optimized hydraulics.
The CYCLOPUR® process is extremely flexible and suitable for all types of wastewater and plant capacities.
Key Features
•Ultraflexible
•Suitable for all types of wastewater and sizes of plant
FLUOPUR®
Moving Bed (MBBR, IFAS)
FLUOPUR® is WABAG’s moving bed process for the biological treatment of wastewater. It can be used as a moving bed (MBBR) on its own or in combination with activated sludge (hybrid or IFAS). The patented carrier material, developed by WABAG, is used to cultivate biofilms capable of performing various tasks according to requirements.
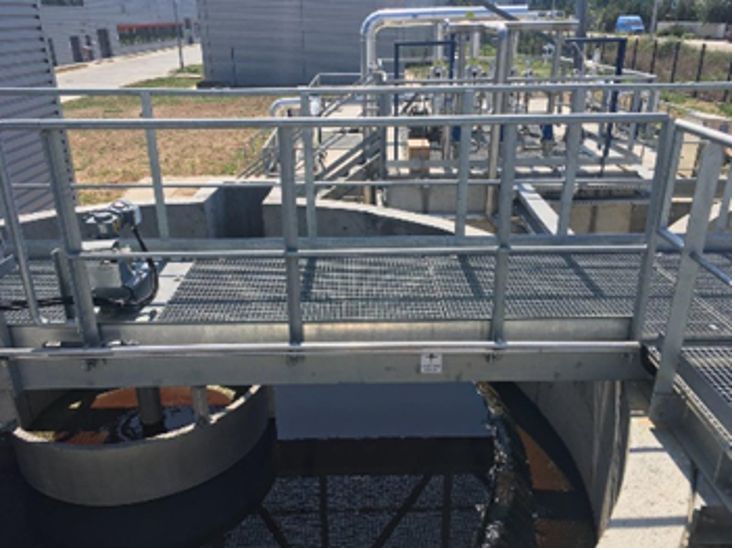
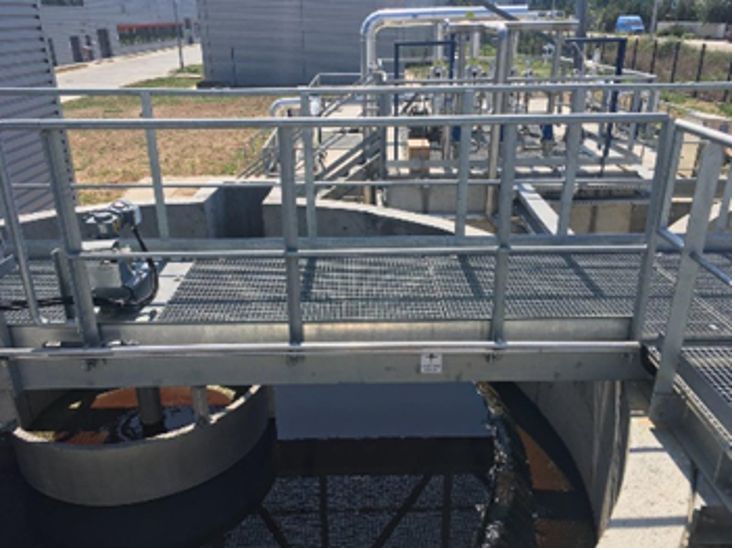
The FLUOPUR® process requires less space than conventional activated sludge treatment, and virtually any tank geometry can be selected. That makes FLUOPUR® ideal for extending existing activated sludge processes when they face capacity bottlenecks or need to meet more stringent purity requirements.
Key Features
•Flexible, straightforward, space-saving system.
•Cost-effective solution for a variety of applications and plant sizes.
•Ideal for extending existing plants (while making use of existing aeration equipment).
•Ideal for industrial wastewater (preliminary/full/secondary treatment).
HYBRID™
The two-stage activated sludge process for nitrogen removal
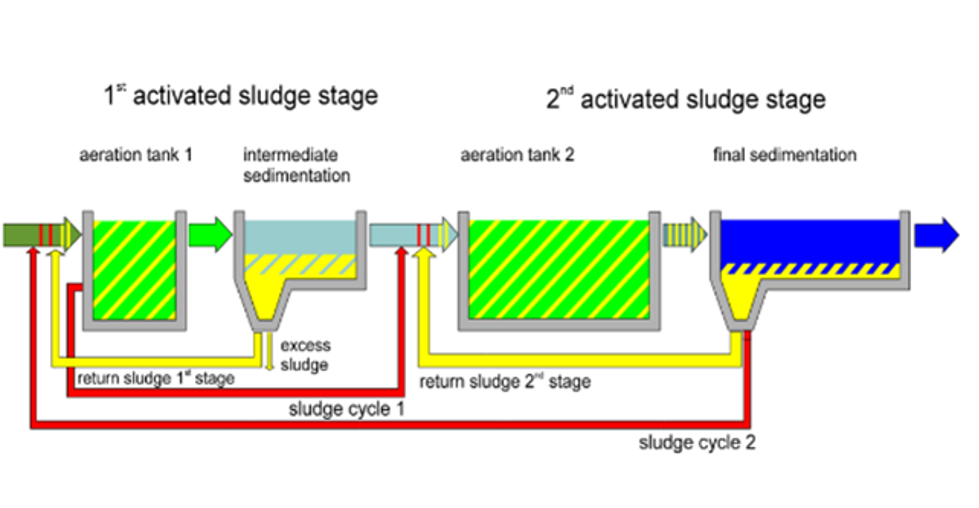
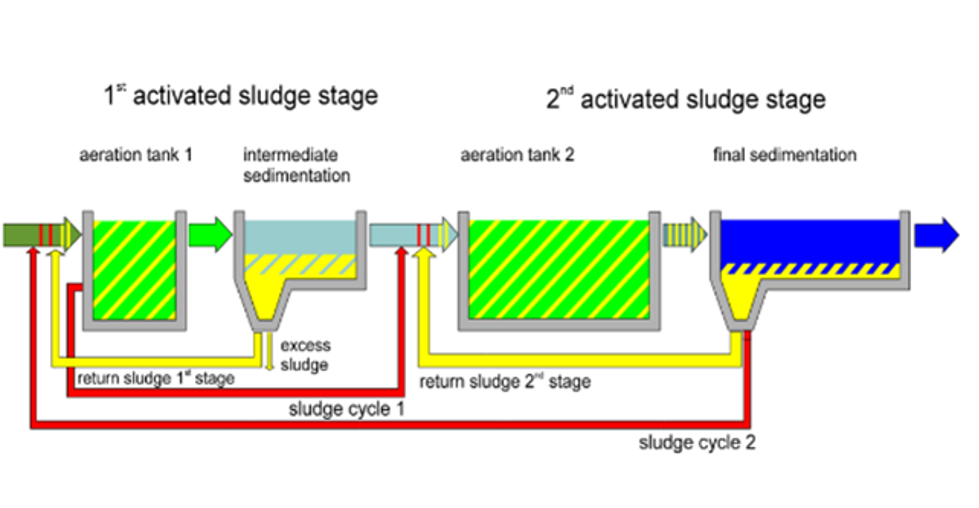
The HYBRID™ process is based on the conventional two-stage activated sludge process. However, the biozenoses of both stages are not separated but advantageously mixed through two innovative hybrid sludge cycles. The process was jointly developed by WABAG and the Vienna University of Technology.
The main advantages are:
Process stability:
The first process stage provides optimum load compensation, securing the denitrification capacity of the second stage even in the case of low wastewater temperatures. This is a crucial advantage, especially when dealing with industrial effluents or seasonal peak loads.
Economies over conventional single-stage plants:
The Hybrid process enables a significant reduction in the required tank volume. Design comparisons for various plants have shown that, in terms of total volume, approximately 30% can be saved..
Key Features
Innovative HYBRID-sludge cycles:
•Combined biozenosis in both stages,
•Nitrification and denitrification in both stages
Flexible way of operation:
•Single stage / two stage,
•Optimum adaptation facilities
Advantages regarding operation costs
Protection against toxic impacts due to two stage treatment
Better hygienization
Ideal for plant extension:
•High flexibility regarding the layout
•Cost-effective possibilities of integrating existing tanks
MARAPUR ®
Membrane Bioreactors (MBR)
Membrane bioreactors (MBR) are powerful systems for the biological treatment of wastewater. The biological treatment stage performs a role similar to a conventional activated sludge system. However, instead of separating activated sludge and clean wastewater in a secondary sedimentation tank by gravity, membrane filtration is employed. As a result, the filtrate contains no solid matter and virtually no bacteria and microorganisms. Additionally, the concentration of sludge in the activated sludge tanks is not limited by the performance of the secondary sedimentation system, allowing for work with higher sludge concentrations. This results in complete solutions that are highly compact.
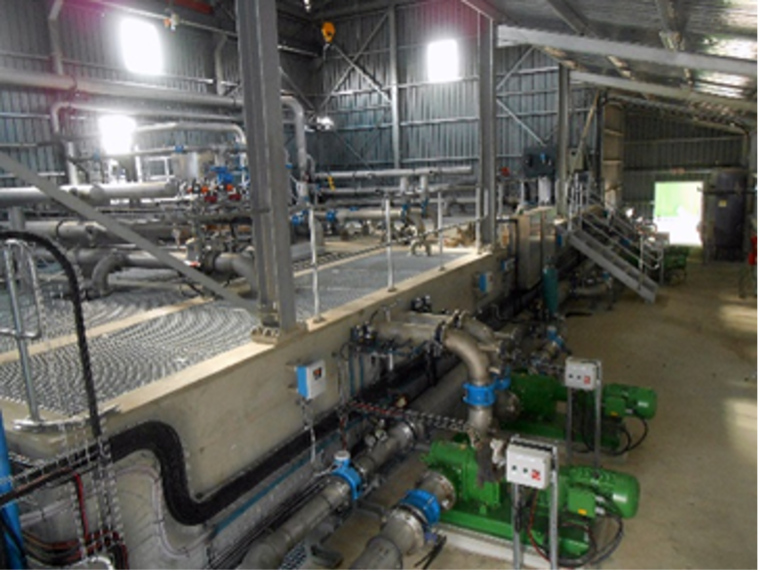
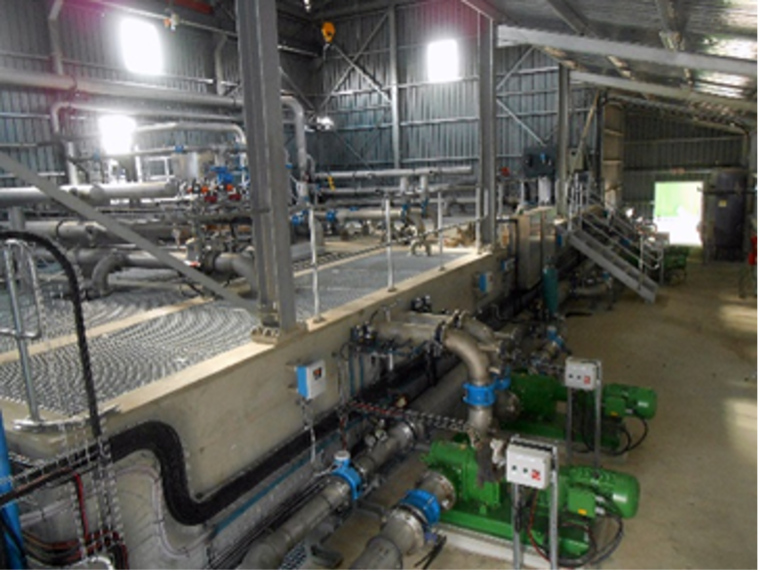
Membrane bioreactors are often the technology of choice for meeting stringent purity requirements. They can also effectively enhance the performance of existing plants. Suitable for municipal and industrial wastewater treatment applications, membrane bioreactors are a key technology for water reuse. A specific preliminary treatment method can be incorporated to ensure appropriate operation and create a straightforward and economical membrane filtration solution..
MARAPUR® MBR plants from WABAG are characterized by a concept that optimizes energy consumption and maximizes membrane life. The company is among the leaders in this technological area, providing ideal solutions for every situation through a diversity of solutions. WABAG’s long-term experience with the operation of large-scale MBR plants is continually updated with further developments, including the optimization of pre-treatment systems (MICROPUR®).
Key Features
•Highly efficient system with minimal space requirements
•Clean wastewater of superb quality, ideal for sensitive receiving waters
•High operational safety even in the event of load changes
•Better degradation of micropollutants
•Easy extension of existing plants
•Perfect in combination with MICROPUR®
MICROPUR®, MICROPUR-MBR®, MICROPUR-CAS®
Advanced mechanical pre-treatment
MICROPUR® represents an advanced mechanical pre-treatment method. This innovative fine sieving process eases the burden on downstream treatment processes by effectively eliminating coarse contaminants, such as hair and fibers, from the wastewater. Furthermore, it significantly reduces suspended solids and, consequently, other undesirable nutrients. When employed upstream of a biological treatment process, it can achieve screening equivalent to primary sedimentation but with minimal space requirements. The MICROPUR® process seamlessly integrates with plants utilizing membrane bioreactors (MICROPUR-MBR®) or conventional activated sludge processes (MICROPUR-CAS®).
Key Features
•Facilitates biological treatment by reducing suspended solids and unwanted nutrients
•Decreases the amount of energy required for biological wastewater treatment
•Enhances gas production during digestion
•Improves operational safety
•Facilitates sludge thickening Requires minimal space
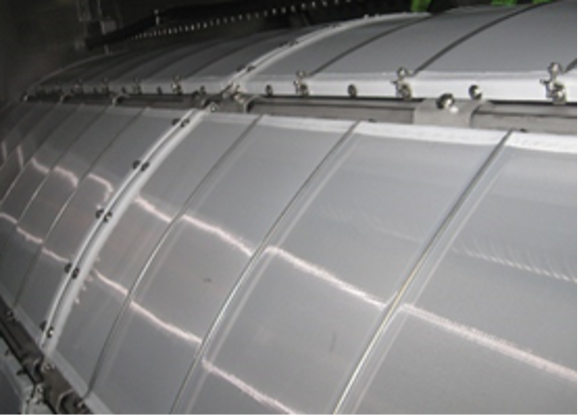
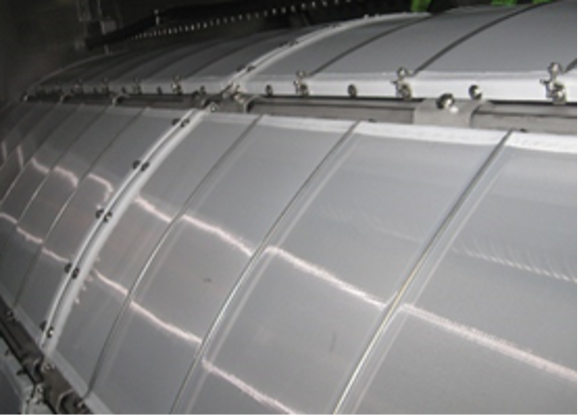
NEREDA® (licensee)
Aerobic Granular Activated Sludge
NEREDA® is a highly advanced technology for biological wastewater treatment based on the SBR method, harnessing the power of aerobic granular sludge. With this technology, bacteria naturally grow in compact granules instead of in flocs.
These granules have excellent settling properties, offering numerous advantages: the biomass concentration in the reactor is very high, but the sedimentation phase is extremely short. Moreover, the reactor can be filled while clear water is being extracted. This results in excellent biological performance, allowing virtually all of the cycle time to be spent on biological processes, leading to small reactors with minimal space requirements. Another key factor is that many biological processes take place within the compact granules simultaneously. This results in high rates of nitrogen and biological phosphorus removal, largely eliminating the need for precipitating agents. Compared to conventional SBR technology, these systems are much more compact overall and produce a better quality of effluent.
Key Features
•Compact plants with minimal space requirements (around 50% compared to SBR).
•Flexibility of a batch process (SBR).
•High rates of biological nutrient removal.
•A proven and robust process with minimal consumption of resources (energy, chemicals) characterized by its ease of operation.
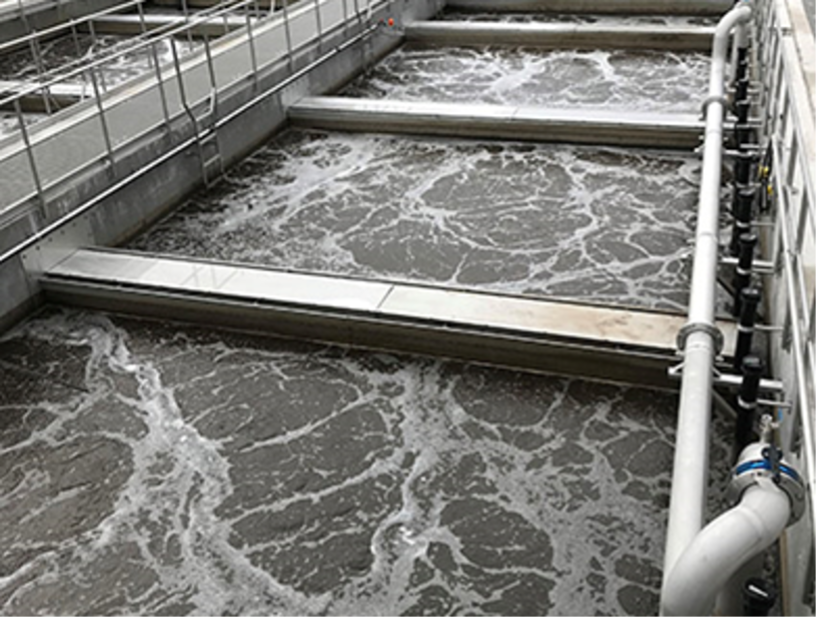
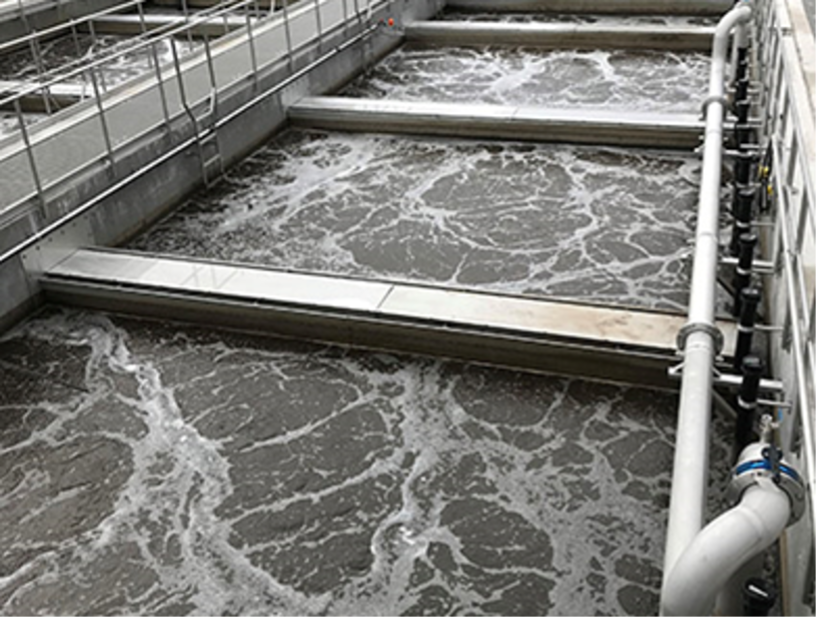
OPUR-SK™
Advanced sedimentation
WABAG has developed this technology in the 1980s with the aim to reduce the footprint of clarifiers after the flocculation and coagulation treatment steps. Having been launched, the WABAG lamella clarifiers have been implemented on numerous drinking water production plants and for effective pre-treatment in municipal and industrial wastewater treatment plants.
The flocculated inlet water is fed to the lamella plates. The particles settle to the lamella plates and slide downward, to be thickened at the bottom of the settler. Whereas the clarified water is collected in to chutes to leave the settler. The lamella plates are in a corrosion and UV-resistant material. They are fixed using a stainless steel structure.
Key Features
•Small footprint
•Proven technology
•Integrated sedimentation of flocculated sludge
•Integrated sludge thickening
•Simplified civil structure
•High process stability
•Flexible operation
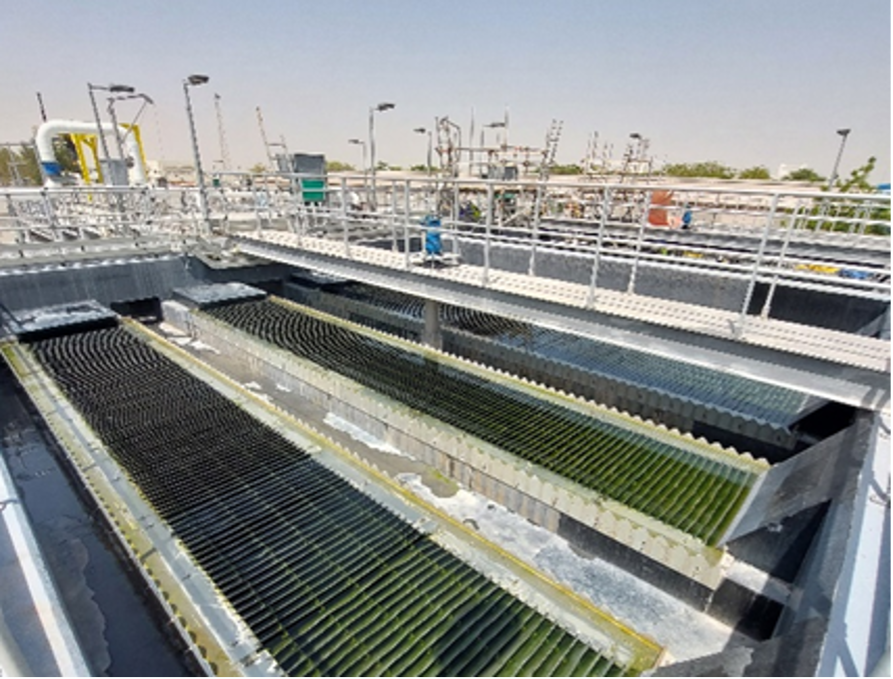
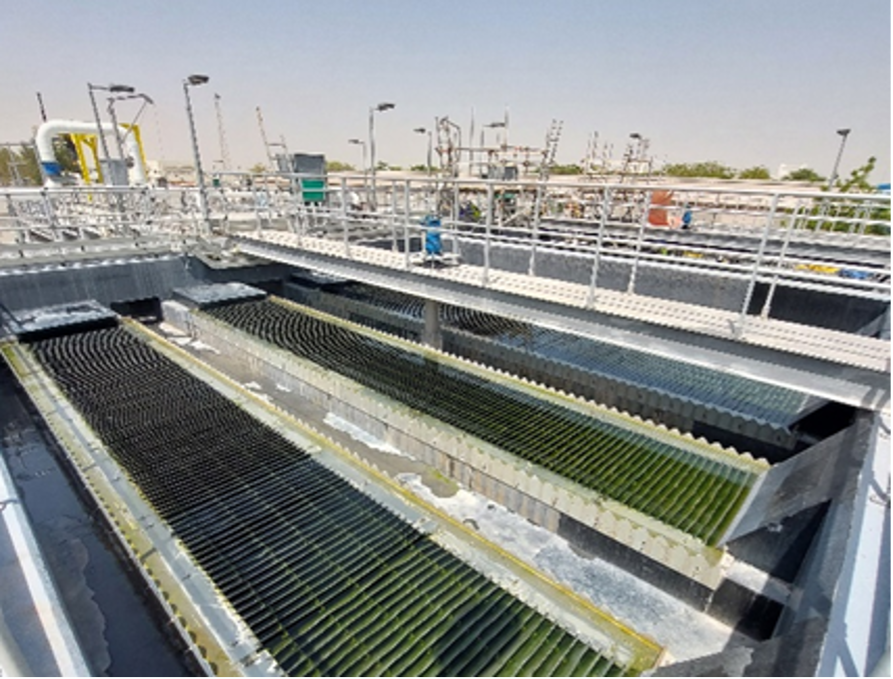